Understanding the 3D Printing Landscape: A Guide for Beginners and Professionals
3D printing has revolutionized the way we approach design and manufacturing, offering unprecedented flexibility and customization. Whether you’re a hobbyist, a designer, or a business looking for rapid prototyping solutions, choosing the right 3D printing technology is crucial. Among the most popular methods are Fused Deposition Modeling (FDM) and Stereolithography (SLA). Each has its unique strengths and applications, but which one is right for you? In this comprehensive guide, we’ll delve into the nuances of FDM and SLA printing technologies to help you make an informed decision.
What is FDM 3D Printing? Advantages, Disadvantages, and Applications
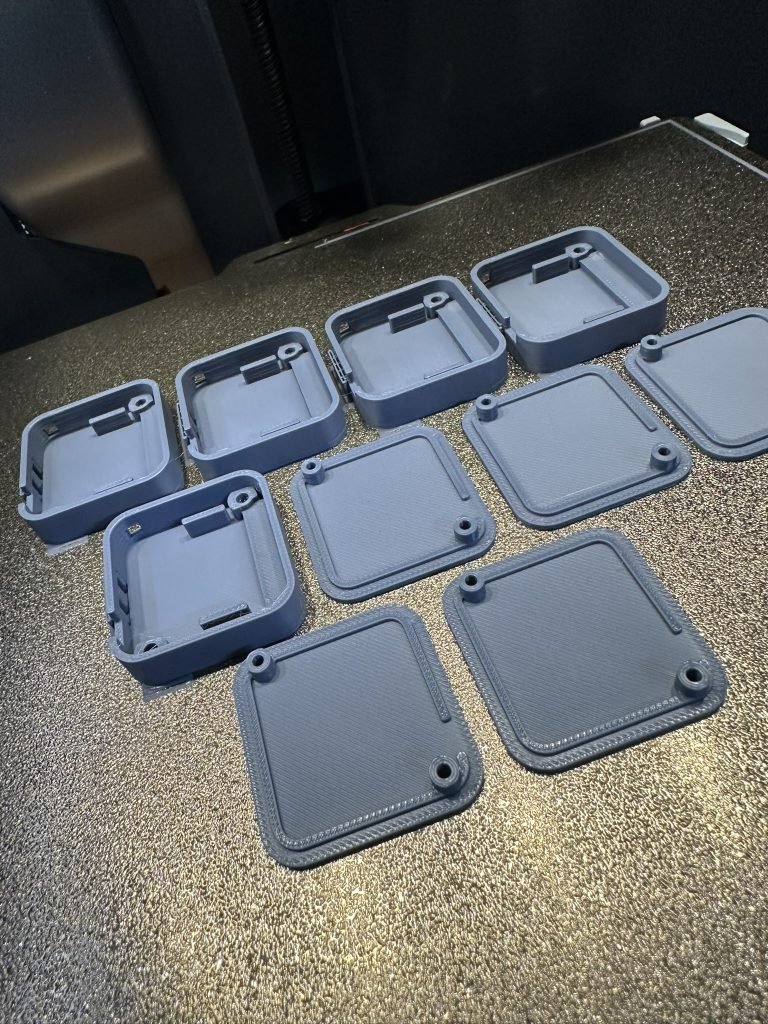
FDM, or Fused Deposition Modeling, is one of the most widely used 3D printing methods, known for its simplicity and cost-effectiveness. Here’s a closer look at what makes FDM a popular choice:
How Does FDM 3D Printing Work?
FDM works by extruding thermoplastic filaments through a heated nozzle. The printer lays down the material layer by layer, building the object from the bottom up. This method is straightforward and relatively inexpensive, making it accessible for various applications.
Benefits of FDM 3D Printing: Cost-Effective and Versatile Solutions
- Cost-Effective: FDM printers and materials are generally cheaper than other 3D printing technologies.
- Wide Range of Materials: FDM supports a variety of materials, including PLA, ABS, PETG, and more specialty options like carbon fiber-infused PETG. Explore our FDM materials for more details.
- User-Friendly: The technology is easy to use, with many open-source options available, making it ideal for beginners.
- Durability: FDM prints are robust and suitable for functional prototypes and end-use parts.
Drawbacks of FDM 3D Printing: Understanding the Limitations
- Surface Finish: FDM prints typically have visible layer lines, which may require post-processing for a smoother finish.
- Detail Resolution: While suitable for many applications, FDM may not achieve the high detail and precision required for intricate designs.
What is SLA 3D Printing? Precision, Applications, and Pros & Cons
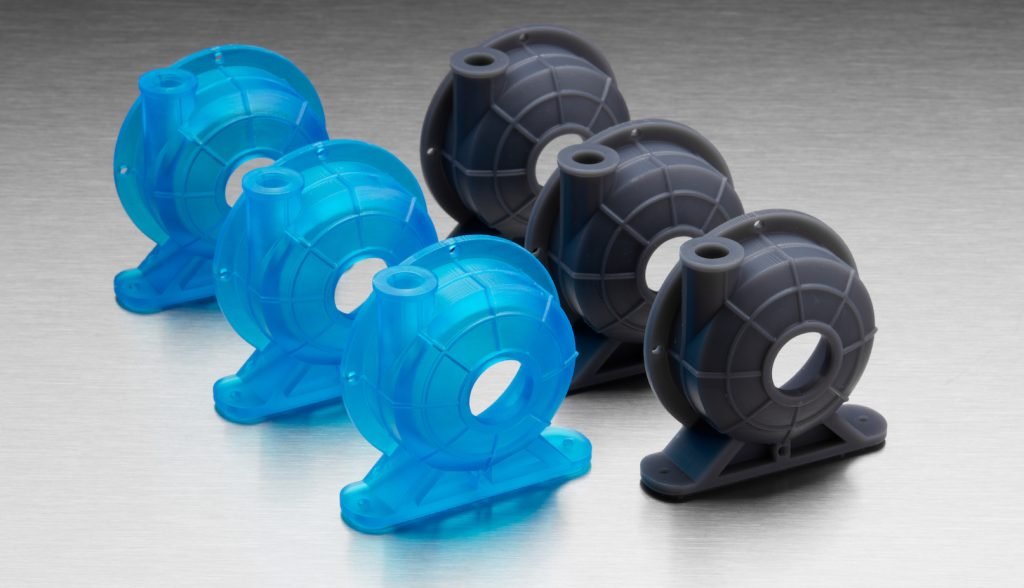
SLA, or Stereolithography, offers a different approach to 3D printing, focusing on precision and high-quality finishes. Here’s what you need to know about SLA:
How Does SLA 3D Printing Work? Detailed Process Explained
SLA printing uses a UV laser to cure liquid resin into hardened plastic. The printer traces the object’s cross-section on the resin’s surface, solidifying each layer before moving to the next. This process allows for exceptionally fine details and smooth surfaces.
Benefits of SLA 3D Printing: High Precision and Quality Finishes
- High Precision: SLA can produce highly detailed and intricate parts, making it ideal for prototypes requiring fine features.
- Smooth Surface Finish: SLA prints have a smoother surface finish right out of the printer, reducing the need for extensive post-processing.
- Material Versatility: SLA offers a variety of resins, including high-detail and functional options. Learn more about our SLA materials.
Drawbacks of SLA 3D Printing: Cost and Post-Processing Challenges
- Cost: SLA printers and resins are generally more expensive than FDM.
- Post-Processing: SLA prints often require post-curing and support removal, adding time to the production process.
- Material Properties: While SLA resins can be highly detailed, they may not offer the same durability and flexibility as FDM filaments.
FDM vs. SLA 3D Printing: Key Factors to Consider When Choosing
When deciding between FDM and SLA, consider the following factors to determine which technology aligns with your needs:
1. Application Requirements
- Prototypes and Functional Parts: FDM is ideal for producing strong, functional prototypes and parts that can withstand mechanical stress. Check out our FDM printing services for more information.
- Detailed Models and Complex Geometries: If your project demands high precision and intricate details, SLA is the way to go. Visit our SLA printing page for more details.
2. Budget Constraints
- Initial Investment and Running Costs: FDM is generally more budget-friendly, both in terms of printer costs and material expenses. However, consider the potential need for post-processing equipment for SLA, which can add to the overall cost.
3. Material Properties
- Strength and Durability: FDM materials like ABS and PETG are known for their strength and durability, making them suitable for functional applications. Explore our range of FDM materials, including high-performance options like carbon fiber PETG.
- Detail and Finish: SLA materials provide excellent detail and surface finish, which is ideal for aesthetic models and precise prototypes. Learn more about our SLA high-detail resin.
4. Production Volume
- Large Batch Production: FDM is often preferred for large batch production due to its speed and cost-effectiveness.
- Small, Detailed Runs: SLA excels in small batch production where detail and surface finish are paramount.
Comparison table for FDM and SLA printing technologies
Feature | FDM (Fused Deposition Modeling) | SLA (Stereolithography) |
Printing Process | Extrudes melted thermoplastic filament layer by layer. | Uses a UV laser to cure liquid resin layer by layer. |
Cost | Generally more cost-effective. Lower printer and material costs. | Typically more expensive. Higher printer and resin costs. |
Print Speed | Moderate to fast, depending on the complexity and size of the object. | Slower, especially for detailed or large prints. |
Surface Finish | Visible layer lines; require post-processing for a smooth finish. | Smooth surface finish right out of the printer; minimal post-processing required. |
Detail and Precision | Suitable for functional parts but limited in fine details. | Excellent for high-detail and intricate designs. |
Material Options | Wide variety of thermoplastics, including PLA, ABS, PETG, and composites like carbon fiber. | Various resins, including standard, high-detail, functional, biocompatible, and specialty resins. |
Durability | Strong and durable prints, suitable for functional parts and prototypes. | Generally less durable than FDM; suitable for detailed models and prototypes requiring high precision. |
Post-Processing | Requires support removal, sanding, filling, and painting. | Requires support removal, washing, and UV curing. |
Applications | Prototyping, custom tooling, jigs, educational models, functional parts. | Dental and medical models, jewelry design, miniatures, artistic models, detailed prototypes. |
Ease of Use | User-friendly, especially with auto-bed leveling and integrated monitoring systems. | Requires careful handling of resin and more complex post-processing steps. |
Environmental Impact | Options for eco-friendly filaments; generally less wasteful. | Resin disposal requires careful handling; environmental impact depends on resin type. |
Printer Maintenance | Relatively low maintenance; regular cleaning of nozzles and bed leveling. | Requires regular cleaning and careful handling of resin and curing systems. |
Print Size | Can print large objects, limited only by printer bed size. | Typically limited to smaller build volumes compared to FDM. |
Material Properties | Materials like ABS and PETG offer high strength and durability. | Specialized resins can offer high detail, flexibility, or biocompatibility. |
Usage Environment | Suitable for home, office, and industrial environments. | Typically used in more controlled environments due to resin handling. |
Learning Curve | Easy for beginners, with many resources and community support available. | Steeper learning curve due to resin handling and post-processing steps. |
Versatility | Highly versatile, suitable for a wide range of applications. | Best for applications requiring high detail and precision. |
Real-World Applications of FDM and SLA: Case Studies and Practical Examples
FDM technology has a broad range of applications across various industries due to its versatility and affordability. Here, we’ll explore some real-world examples where FDM has proven to be the ideal choice:
FDM 3D Manufacturing Prototypes
In the manufacturing industry, the ability to rapidly prototype and iterate designs is crucial. FDM’s cost-effectiveness and ease of use make it an excellent choice for creating functional prototypes. For instance, automotive companies often use FDM to develop and test parts before committing to expensive tooling.
FDM 3D Printing Case Study: Prototyping Automotive Parts
A leading automotive manufacturer needed to prototype a new car part with specific durability requirements. Using FDM, they were able to produce several iterations quickly and at a low cost. The use of FDM ABS allowed them to create prototypes that withstood rigorous testing, significantly reducing the time and cost associated with traditional prototyping methods.
FDM 3D Printing for Custom Tooling and Jigs: Efficiency and Durability
Manufacturing processes often require custom tools and jigs. FDM is particularly well-suited for producing these items because of its strength and material variety.
FDM 3D Printing Case Study: Enhancing Assembly Line Efficiency with Custom Jigs
A consumer electronics company utilized FDM to create custom jigs for their assembly line. By using durable materials like FDM PC, they produced jigs that enhanced the efficiency and accuracy of their assembly process. The quick turnaround and low cost were significant advantages, allowing for rapid adjustments and improvements.
FDM 3D Printing in Education: Creating Detailed Educational Models
FDM is widely used in education for creating models that help in teaching complex concepts. From anatomical models in medical schools to architectural designs in engineering courses, FDM provides a tangible way to bring theoretical concepts to life.
FDM 3D Printing Case Study: Medical Training Models for Enhanced Learning
A medical school needed detailed anatomical models for student training. They opted for FDM due to its affordability and the variety of available materials. Using FDM PLA, they created durable models that helped students better understand human anatomy through hands-on learning.
SLA 3D Printing Applications: High-Precision Uses in Various Fields
SLA technology excels in applications requiring high precision, fine details, and smooth surface finishes. Here are some examples of where SLA shines:
SLA Printed Dental and Medical Models
SLA’s precision and ability to produce smooth surfaces make it ideal for dental and medical applications. This includes creating accurate dental molds and surgical guides.
SLA 3D Printing Case Study: Precision Dental Impressions
A dental lab is needed to produce highly accurate dental impressions for custom dental implants. Using SLA, they were able to create detailed models with smooth finishes, ensuring a perfect fit for each patient. The use of SLA high-detail resin provided the necessary accuracy and detail, significantly improving patient outcomes.
SLA 3D Printing for Jewelry Design: High-Detail Casting Prototypes
The jewelry industry often requires highly detailed models for casting. SLA’s ability to produce intricate designs with fine details makes it perfect for this application.
SLA 3D Printing Case Study: Creating Intricate Jewelry Prototypes
A custom jewelry designer utilized SLA to create prototypes of intricate pieces. The high precision and smooth surface finish of SLA allowed them to present highly detailed models to clients, leading to a higher approval rate before moving to the casting stage. This process not only saved time but also reduced material waste.
SLA 3D Printing for Miniatures: Creating High-Detail Artistic Models
Artists and designers often require models with fine details and a high-quality finish. SLA’s capabilities make it an excellent choice for creating miniatures and other artistic models.
SLA 3D Printing Case Study: Detailed Tabletop Game Miniatures
A company producing miniatures for tabletop games chose SLA to create detailed characters and scenery pieces. The smooth finish and high level of detail achievable with SLA enhanced the aesthetic appeal of the miniatures, leading to increased customer satisfaction and sales. Using various SLA resins, they were able to achieve the desired results consistently.
EXCELLENT Based on 3 reviews Andy Ireland2023-03-16 Excellent quality and fast service, best 3D print service I've used. Andy Jary2023-01-19 Excellent company and the best value I've found for 3D Printing. I ordered 2 replacement battery door covers for a Texas Instruments Speak & Spell. Arrived in no time, in perfect condition and fitted perfectly. Thank you! Andrew Sidwell2022-07-11 I needed a spare part for a Siemens microwave oven, long out of production and most parts no longer available. I found an stl file online and 3drevolution made the part in ABS, stronger than the original and cheaper. Excellent service - quick turnaround and very good prices.
How to Choose Between FDM and SLA 3D Printing for Your Project
When deciding between FDM and SLA, consider the specific requirements of your project. Here are some key points to help you choose:
- For Cost-Effective, Durable Parts: FDM is the best choice for creating robust, functional prototypes and parts. Its affordability and material variety, including FDM PETG and carbon fiber PETG, make it versatile and accessible.
- For High-Detail, Smooth Finish Models: SLA is ideal for applications requiring high precision and a smooth surface finish. Whether you need detailed dental models or artistic miniatures, SLA’s capabilities ensure top-notch results.
Customizing Your 3D Printing Solution: FDM and SLA at 3DRevolution.co.uk
At 3DRevolution.co.uk, we offer both FDM and SLA printing services to meet a diverse range of needs. Whether you’re developing a functional prototype or creating intricate designs, our team can help you choose the right technology and materials for your project. Visit our services page to explore our offerings and get started on your 3D printing journey.
Post-Processing Techniques for FDM and SLA Prints: Tips and Best Practices
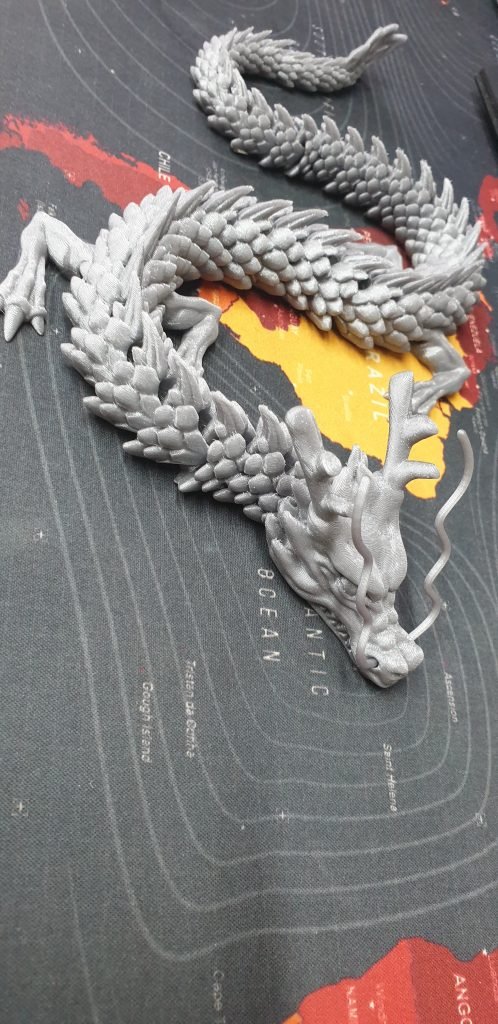
Essential Guide to Post-Processing 3D Prints
Post-processing is an essential step in 3D printing, enhancing the quality and functionality of printed parts. Both FDM and SLA prints benefit from post-processing, though the techniques and tools used vary. In this section, we’ll cover the best practices for achieving professional results with your FDM and SLA prints.
How to Post-Process FDM 3D Prints
FDM prints often require post-processing to improve their appearance and functionality. Here are some common techniques:
- Removing Support Structures from FDM 3D Prints: Methods and Tools
Support structures are necessary for printing overhangs and complex geometries but need to be removed once printing is complete.
- Manual Removal: Use pliers or a cutter to carefully remove support structures. Ensure you don’t damage the print in the process.
- Automated Tools: For large volumes, consider using an automated support removal system to speed up the process.
- Sanding FDM 3D Prints: Achieving a Smooth Finish
Sanding helps to smooth the surface of FDM prints, especially if there are visible layer lines.
- Start with Coarse Grit: Begin with a coarse grit (e.g., 80-100) to remove significant imperfections.
- Progress to Finer Grit: Gradually move to finer grits (e.g., 220-320) to achieve a smoother finish. For a polished look, consider wet sanding with very fine grit (e.g., 600-1200).
- How to Fill Gaps and Seams in FDM 3D Prints: Best Techniques
Filler materials can be used to smooth out gaps and seams in FDM prints.
- Epoxy or Putty: Apply a thin layer of epoxy or putty to fill gaps. Once dried, sand it down to blend with the rest of the surface.
- Priming: After filling and sanding, apply a primer to prepare the surface for painting or further finishing.
- Painting FDM 3D Prints: Tips for a Professional Look
Painting enhances the appearance of FDM prints, giving them a professional look.
- Surface Preparation: Ensure the surface is clean and smooth before painting. Use a primer if necessary.
- Painting Techniques: Apply thin, even coats of paint. Spray painting often provides the best finish. Consider using acrylic or enamel paints for durability.
- Chemical Smoothing Techniques for FDM 3D Prints: Achieving a Polished Finish
Chemical smoothing can significantly improve the surface finish of FDM prints, particularly for materials like ABS.
- Acetone Vapor Bath: For ABS prints, an acetone vapor bath can smooth the surface by slightly melting the outer layer. This method should be used with caution and proper ventilation.
- Commercial Solutions: There are commercial smoothing solutions available for other materials, such as PLA, which can be applied using a brush or dip method.
How to Post-Process SLA 3D Prints: Best Practices Guide
SLA prints typically have a finer surface finish out of the printer, but they still benefit from post-processing to achieve optimal results.
- Removing SLA Print Support Structures
Similar to FDM, SLA prints often require support structures that need removal.
- Manual Removal: Carefully cut away support structures with a scalpel or fine-tipped cutters. Be gentle to avoid damaging delicate features.
- Sanding: Lightly sand the areas where supports were attached to smooth out any imperfections.
- Washing and Curing SLA 3D Prints: Step-by-Step Process
SLA prints are often sticky when they come out of the printer due to uncured resin. Washing and curing are critical steps to finalize the print.
- Isopropyl Alcohol (IPA) Bath: Wash the print in an IPA bath to remove excess resin. Use a soft brush to ensure all resin is removed from intricate details.
- Post-Curing: Cure the print under UV light to fully harden the resin. This step is crucial for achieving the material’s full mechanical properties. Refer to the manufacturer’s guidelines for specific curing times.
- Sanding and Polishing SLA 3D Prints: Achieving a High-Quality Finish
For an ultra-smooth finish, sanding and polishing SLA prints can be effective.
- Progressive Sanding: Start with fine-grit sandpaper (e.g., 400-600) and move to higher grits (e.g., 1000-2000) for a smooth finish. Wet sanding is recommended to avoid dust.
- Polishing: Use a polishing compound to achieve a glossy finish, especially if the print is clear or needs a high aesthetic quality.
- Painting and Coating SLA 3D Prints: Enhancing Appearance and Durability
Painting SLA prints can add color and protect the surface.
- Priming: Apply a primer designed for resin to ensure good paint adhesion.
- Painting: Use thin, even coats of paint. Spray painting works well for even coverage.
- Coating: For additional protection and a glossy finish, consider applying a clear coat or varnish.
Expert Tips for Perfecting Your 3D Prints: From FDM to SLA
Effective post-processing is key to transforming your 3D prints from good to great. By following these best practices for FDM and SLA post-processing, you can enhance the appearance, functionality, and durability of your prints. At 3DRevolution.co.uk, we provide detailed design guides and support to help you achieve the best results with your projects. Visit our materials page to explore the full range of materials and get started on your next 3D printing project.
Future Trends in FDM and SLA Printing Technologies: What to Expect
Latest Advancements in FDM 3D Printing Technology
As 3D printing technologies continue to evolve, both FDM and SLA are seeing significant advancements that promise to enhance their capabilities and expand their applications. In this final section, we will explore the future trends in FDM and SLA printing technologies, providing insights into what you can expect in the coming years.
Advancements in FDM Technology
FDM technology is continually improving, with developments focused on enhancing print quality, speed, and material versatility.
- Enhancing Print Speed and Quality in FDM 3D Printing
New advancements in FDM technology aim to significantly increase print speed without compromising quality.
- High-Speed Extruders: Innovations in extruder technology, such as dual-gear and high-flow extruders, are enabling faster print speeds and more consistent filament flow.
- Multi-Material Printing: Advances in multi-material printing allow for the simultaneous use of different filaments, enabling more complex and functional prints. This is particularly beneficial for creating parts with varied mechanical properties or integrated components.
- Exploring New Material Options for FDM 3D Printing
The range of materials available for FDM printing is expanding, offering more options for specialized applications.
- Composite Filaments: The development of new composite filaments, such as metal-infused and carbon fiber-reinforced filaments, provide enhanced strength, durability, and heat resistance.
- Eco-Friendly Materials: As sustainability becomes a priority, eco-friendly filaments made from recycled or biodegradable materials are gaining traction. Explore our selection of FDM materials for the latest options.
- Automation and Smart Features in Modern FDM 3D Printers
Automation and smart features are making FDM printers more user-friendly and efficient.
- Auto-Bed Leveling: Automated bed leveling systems ensure precise first layers, improving print reliability and reducing setup time.
- Integrated Monitoring: Advanced monitoring systems use cameras and sensors to provide real-time feedback on print quality, enabling immediate adjustments and reducing print failures.
Latest Advancements in SLA 3D Printing Technology
SLA technology is also advancing, with a focus on improving precision, material properties, and accessibility.
- Achieving Higher Precision and Detail in SLA 3D Printing
SLA printers are achieving higher levels of precision and detail, opening new possibilities for intricate designs.
- Higher Resolution Lasers: New developments in laser technology allow for finer details and smoother surfaces, enhancing the aesthetic quality of SLA prints.
- Micro-SLA Printing: Micro-SLA technology enables the production of incredibly detailed microstructures, useful in fields like medical device manufacturing and microelectronics.
- New Material Capabilities for SLA 3D Printing
SLA materials are evolving to meet the demands of more diverse applications.
- Functional Resins: The development of new functional resins, such as high-temperature and impact-resistant resins, broadens the scope of SLA applications. Discover our range of SLA materials for more details.
- Biocompatible and Specialized Resins: Innovations in biocompatible and other specialized resins are making SLA suitable for medical and dental applications, where safety and performance are critical.
- Improving Accessibility and User Experience in SLA 3D Printing
Improving accessibility and user experience is a key focus for SLA technology.
- User-Friendly Interfaces: Modern SLA printers feature intuitive interfaces and software that simplify the printing process, making it more accessible to beginners and professionals alike.
- Automated Post-Processing: Integrated solutions for automated washing and curing streamline the post-processing workflow, reducing the manual effort required and ensuring consistent results.
The Future of 3D Printing with 3DRevolution.co.uk: What’s Next?
At 3DRevolution.co.uk, we are committed to staying at the forefront of 3D printing technology. By continually updating our equipment and expanding our material offerings, we ensure that our clients have access to the latest advancements in FDM and SLA printing. Whether you are looking to create durable prototypes with advanced FDM materials or intricate designs with high-precision SLA resins, we have the solutions to meet your needs.
Embrace the Future of 3D Printing: FDM and SLA Innovations
The future of FDM and SLA printing technologies is bright, with ongoing advancements driving improvements in speed, quality, and versatility. By staying informed about these trends and adopting the latest innovations, you can take full advantage of what 3D printing has to offer. At 3DRevolution.co.uk, we are here to support you with cutting-edge technology and expert guidance. Visit our services page to learn more about how we can help you achieve your 3D printing goals.
Final Thoughts: Choosing Between FDM and SLA for Your 3D Printing Needs
Choosing between FDM and SLA printing technologies depends on your specific needs and project requirements. By understanding the strengths and limitations of each, and staying updated on the latest advancements, you can make informed decisions that will enhance your 3D printing projects. Whether you’re looking to create robust prototypes or highly detailed models, 3DRevolution.co.uk is your partner in bringing your ideas to life.
Explore More 3D Printing Resources at 3DRevolution.co.uk:
- FDM Printing Services
- SLA Printing Services
- FDM Materials
- 3D Printing Blog
- SLA High-Detail Resin
- Carbon Fiber PETG
- ASA Material
We hope this guide has provided valuable insights into FDM and SLA printing technologies, helping you choose the right method for your next project. For more information and to start your 3D printing journey, visit 3DRevolution.co.uk.