(PETg) Polyethylene terephthalate glycol
- Lead time < 5-10 days
3D printing technology:
Specifications
Colors
And more
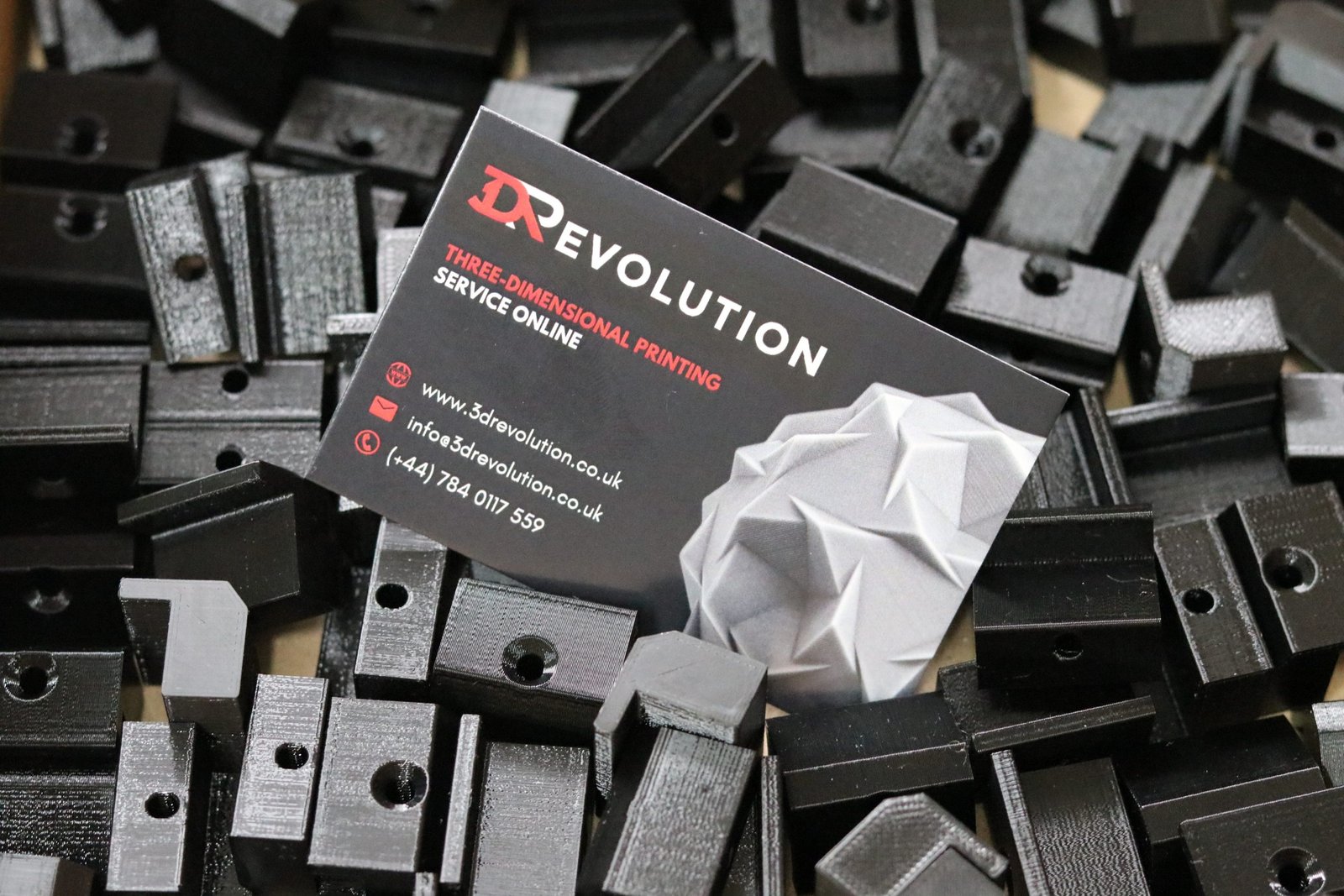
About 3D Printing Material - Polyethylene terephthalate PET (PETG)
The perfect all-round plastic for your prototyping needs. PETG is a popular 3D printer filament. The ‘G’ stands for “glycol-modified”, and the result is a filament which is clearer, less brittle, and most importantly, easier to use than its base form. For this reason, PETG is often considered a good middle ground between ABS and PLA, the two most commonly used 3D printer filaments, as it is more flexible and durable than PLA and easier to print than ABS.
The material is strong and extremely versatile, easy to paint and post process making it the perfect choice for almost any 3D printing project.
PETG CHARACTERISTICS:
Tolerances: ±0.5% with a lower limit of ±0.5 mm (±0.020″)
Max Part Size: 450 x 450 x 470 mm
Layer Height: 100 – 300
Infill Options: 20% Standard – 80-100% High Infill
Wall Thickness: 0.8 mm
Strengths | Weaknesses |
---|---|
Low-cost, fast turnaround times | Limited dimensional accuracy, print layers are likely to be visible
|
When Should You Use (PETg) 3D Printing Materials?
PETG is a good all-rounder but stands out from many other filaments due to its flexibility, strength, and temperature and impact resistance. This makes it an ideal 3D printer filament to use for objects which might experience sustained or sudden stress, like mechanical parts, printer parts, and protective components.
RECOMMENDED FOR:
✔ Fit & Form Testing
✔ Functional Prototypes
✔ Electronic Enclosures and Cases
✔ Large Models
✔ End User Products
✔ Batch Manufacturing
✔ Jigs and Fixtures
✔ Architectural Models
NOT SUITABLE FOR:
✘ Jewellery Design
✘ Small and Detailed Art Models (eg. Miniatures and Gaming)
✘ Designs with Large Curved Surfaces (eg. Spherical Objects)
Design guide
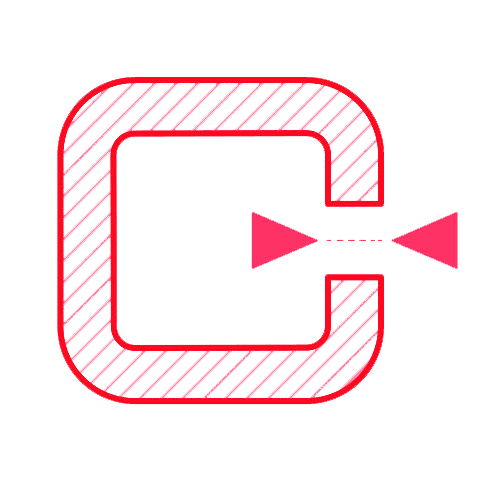
≥ 0.6 mm
Wall Thickness
Vertical features are often overlooked but they play a very important part in whether or not your print will be successful and how strong the final result will be. We always recommend designing walls with a thickness of at least 1 mm with a minimum viable thickness of 0.6 mm.
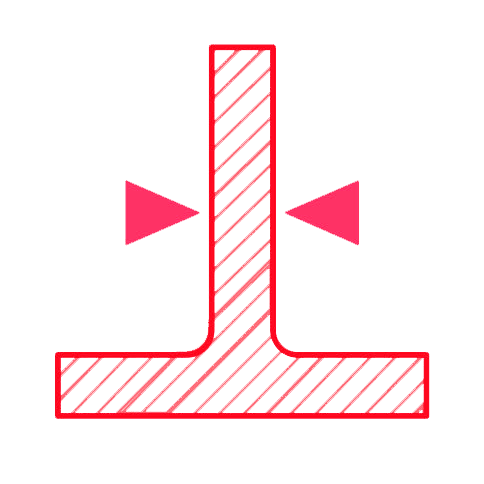
≥ 1.6 mm
Unsupported Wall Thickness
In order to achieve the best results we recommend a minimum thickness of 0.6 mm for unsupported walls.
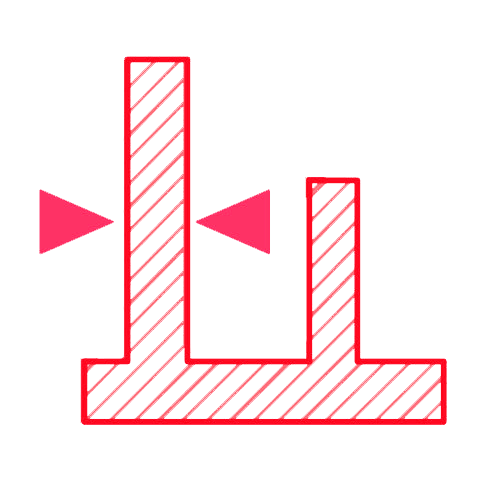
≥ 3 mm
Pillar Diameter
Pins and columns are often used in electronic and end product casings. For best results avoid designing pins with a diameter smaller than 3 mm.
TIP: Adding a chamfer or fillet at the base of your pins will result in much stronger parts.
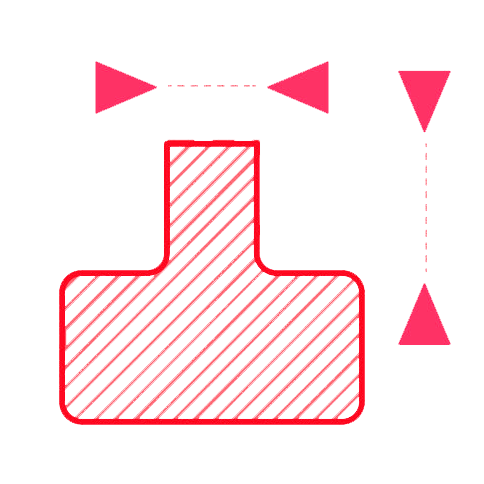
≥ 1.6 mm Thickness
≥ 0.5 mm Depth
Embossed Details
Embossed details should have a minimum line thickness of 1.6 mm and a depth of 0.5 mm or higher.
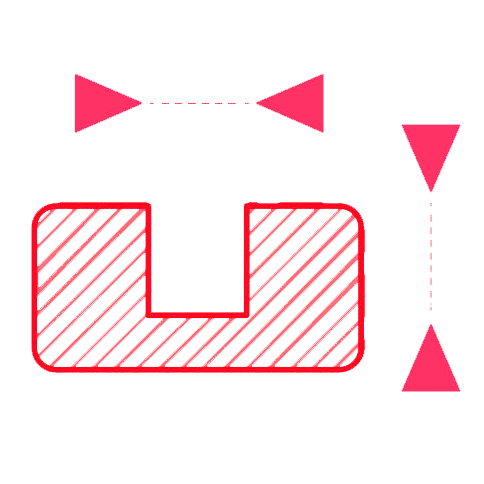
≥ 1.2 mm Thickness
≥ 0.3 mm Depth
Engraved Details
Engraved details require a minimum line thickness of 1.2 mm and a depth of at least 0.3 mm.
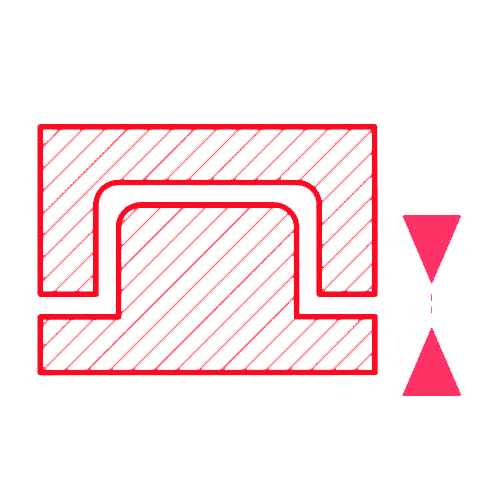
≥ 0.4 mm
Clearance Between Parts
When designing an assembly of parts we suggest leaving a clearance of at least 0.4 mm around moving/sliding parts.
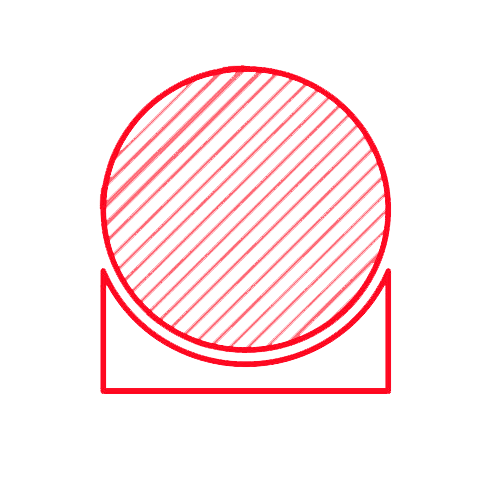
Supports Required
Our PLA / PETG / ABS / PC requires supports in order to print overhanging areas. It’s important to keep this in mind during the design phase since the surface in contact with the support material will exhibit a rougher finish compared with the rest of the model.
Check out our other Printing Materials
SLA 3D Printing material
FDM 3D Printing material
From Prototype to Product – Experience the Durability of PETG!
The Ultimate (PETg) Polyethylene terephthalate glycol FAQ: Strength, Durability, and Versatility
Primary Benefits of Using PETG for 3D Printing
1. Strength and Durability
- PETG offers a unique combination of strength, flexibility, and durability, making it a versatile choice for various 3D printing applications.
- It is less brittle than PLA and easier to print than ABS.
- Exhibits excellent layer adhesion, contributing to the robustness of printed parts.
2. Chemical and Moisture Resistance
- PETG is resistant to moisture, chemicals, and impact, ensuring that printed objects can withstand rigorous use.
3. Ease of Use
- Prints with minimal warping and stringing.
- Does not require a heated chamber, enhancing its appeal for both beginners and advanced users.
4. Versatile Applications
- Ideal for functional prototypes, end-use products, mechanical parts, and outdoor applications.
Comparing PETG to PLA and ABS in Strength and Durability
PETG vs. PLA
- Strength: PETG is stronger and more durable than PLA.
- Temperature Resistance: PETG can endure higher temperatures compared to PLA.
- Flexibility: PETG has greater flexibility, reducing the likelihood of breaking under stress.
PETG vs. ABS
- Ease of Printing: PETG is easier to print with, as it does not emit unpleasant fumes and has a lower tendency to warp during printing.
- Impact Resistance: PETG offers better impact resistance and can withstand sustained mechanical stress.
Applications
PETG’s balance of properties makes it suitable for:
- Robust, functional parts
- Mechanical components
- Protective gear
Limitations of Using PETG in 3D Printing
Dimensional Accuracy
PETG has limited dimensional accuracy compared to more rigid materials like PLA.
Surface Finish
- Layer Lines: Prints tend to have visible layer lines, affecting the aesthetics of the final product.
- Support Structures: PETG requires support structures for printing overhanging features, leading to rougher surfaces where supports are removed.
Post-Processing
Additional post-processing steps, such as sanding and chemical smoothing, may be necessary to achieve a smooth surface.
Achieving the Best Results with PETG
Design Guidelines
- Ensure wall thicknesses are at least 0.8 mm and unsupported walls are a minimum of 1.6 mm thick.
- For pins and columns, maintain a diameter of at least 3 mm and add chamfers or fillets at their bases to enhance strength.
- Proper clearance between moving parts, typically around 0.4 mm, is crucial.
Printing Settings
- Use a heated bed set to 70-80°C.
- Nozzle temperature should be between 230-250°C.
- Optimize retraction settings to minimize stringing.
- Use adequate cooling to prevent overheating.
Post-Processing Techniques
- Sanding and chemical smoothing can improve the finish.
- Carefully plan supports to ensure minimal surface roughness on critical areas.
Industries Benefiting from PETG in 3D Printing
Automotive Industry
PETG is used for creating durable, impact-resistant parts and prototypes.
Consumer Electronics
Strength and ease of use make PETG ideal for manufacturing casings and functional components.
Aerospace and Medical Devices
These industries leverage PETG’s robustness and chemical resistance for various applications, including mechanical parts and protective gear.
Educational Projects
PETG’s safety and versatility make it ideal for creating functional models and hands-on learning aids in STEM education.
Outdoor Applications
PETG’s ability to withstand environmental conditions extends its industrial relevance for outdoor use.
Best Post-Processing Techniques for PETG
Sanding
Sanding can smooth out layer lines and create a more polished surface.
Painting
PETG can be painted, and its chemical resistance means it can be treated with various paints without degrading.
Chemical Smoothing
Using solvents like dichloromethane can enhance surface smoothness.
Gluing
PETG can be glued using standard adhesives, facilitating the assembly of complex multi-part models.
Environmental Benefits of PETG Filament
Recyclability
PETG is fully recyclable, contributing to reduced waste and supporting sustainable manufacturing practices.
Low Emissions
The production of PETG generates fewer emissions and consumes less energy compared to some other plastics.
Durability
PETG’s durability and long lifespan mean parts are less likely to need frequent replacement, reducing the environmental impact.
Impact of PETG on Print Quality and Surface Finish
Print Quality
PETG is known for its high print quality and smooth surface finish.
Layer Adhesion
Excellent layer adhesion ensures strong, cohesive prints with minimal warping.
Appearance
Prints have a glossy appearance, and while layers may be visible, they are typically less pronounced than with some other materials.
Using PETG for Transparent Parts
Transparency
PETG is available in transparent variants, suitable for applications where clarity is essential.
Applications
- Protective covers
- Display cases
- Light fixtures
Advantages
The inherent strength and durability of PETG, combined with its transparency, provide an excellent solution for applications requiring both visibility and robustness.
Suitability of PETG for High-Speed Printing
Performance
Yes, PETG can be used for high-speed printing, though achieving the best results requires careful optimization of printer settings.
Key Adjustments
- Print Speed: Adjusting the print speed is essential to balance speed and quality.
- Temperature Settings: Proper nozzle and bed temperature settings are crucial for consistent extrusion and adhesion.
- Cooling: Adequate cooling helps prevent overheating and maintains print quality.
- Retraction Settings: Ensuring proper retraction minimizes stringing and improves overall print quality.
Applications
By fine-tuning these parameters, PETG can produce high-quality prints efficiently, making it suitable for rapid prototyping and batch manufacturing.
Using PETG in Dual Extrusion 3D Printing
Compatibility
Yes, PETG is compatible with dual extrusion 3D printing, enabling the creation of multi-material or multi-color prints.
Advantages
- Complex Geometries: Dual extrusion allows for the use of soluble support materials like PVA, enabling the printing of complex geometries.
- Enhanced Functionality: Combining PETG with other filaments can produce parts with enhanced functionality and aesthetic appeal.
Applications
Dual extrusion with PETG can be used for advanced 3D printing projects, including:
- Multi-material components
- Intricate designs
- Prototypes requiring multiple material properties